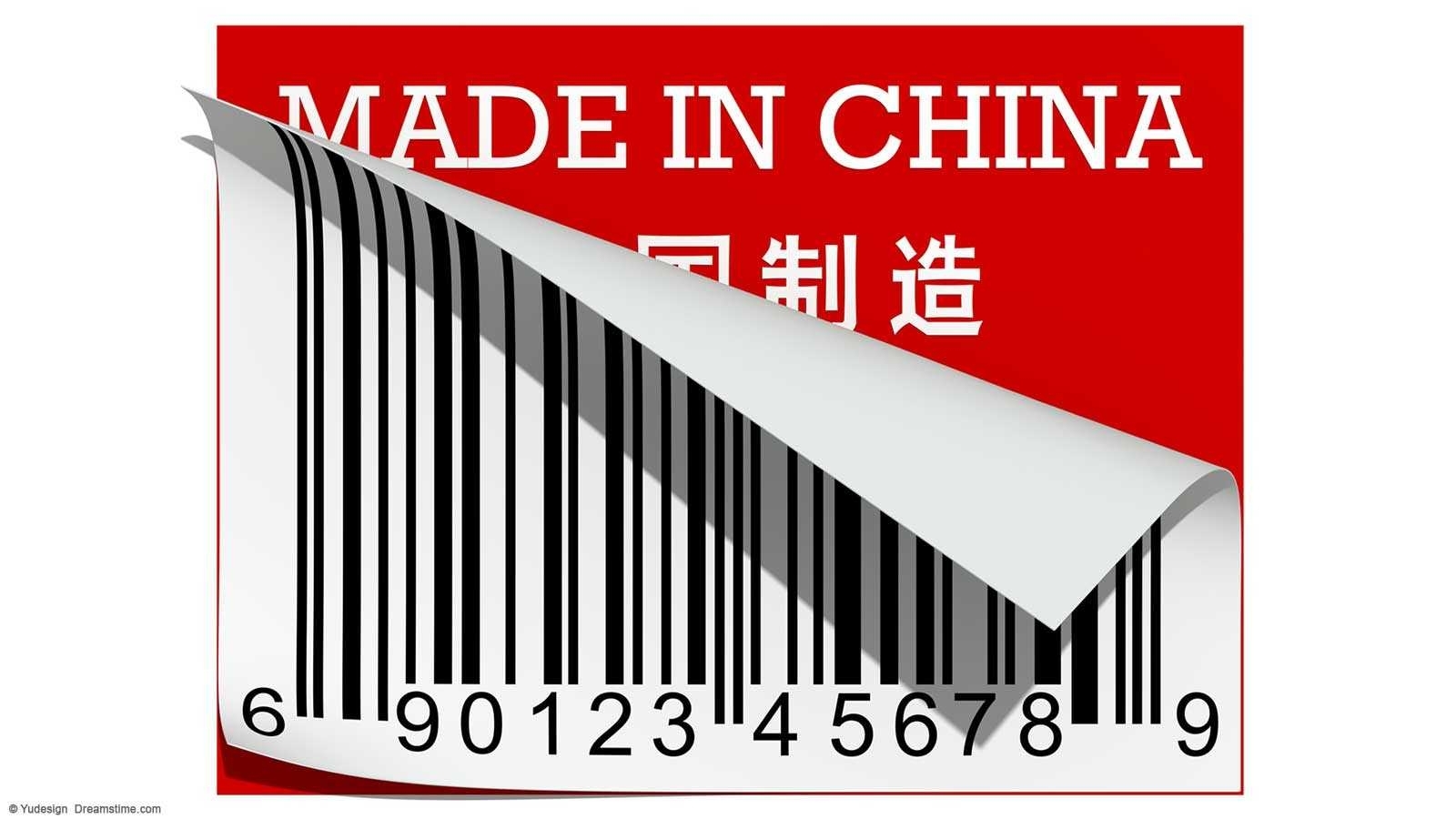
TOPICS:
The Offshoring Frenzy Hangover
Jul 16, 2023 / Written by: Gary Isbell
For more than thirty years, manufacturing trends have favored the developing world and worked against the interests of the United States. Punitive federal and state laws and soaring labor costs coupled with unrealistic union demands made U.S. manufacturing increasingly difficult and foreign production more appealing. But did every company make a sound fiscal decision to move or was it frenetic intemperance that drove their decision?
Many companies sent production to China without ever determining the actual costs and pitfalls of working abroad. There is the problem that marketing and engineering are separated by at least 6,500 miles. This leads to communication issues, increased travel costs to fly abroad to negotiate and solve quality problems and shipping costs, not to mention the fact that Chinese manufacturers steal American technology and undercut the U.S. market.
Communist China has proven itself not to be the manufacturing paradise that some claimed it to be; wages are skyrocketing, workers are fickle, public resistance to environmental devastation is growing, and the state investment led model is showing serious strain. In a theater typical of Chinese bravado, they have “created jobs” by building factories, highways, railroads, dams and airports where there are no cities, and cities where there are no people.
The addition of high tech components to manufactured items further complicates production, making American production more attractive. This is not just because manufacturers now have more proprietary technology to protect, but also because the average American worker is more skilled than their Chinese counterpart. In short, the transition from one product generation to the next makes the chemistry of the team, comprised of marketers, engineers, factory workers and domestic shipping, an important component to the success of any industry.
Consider a few of the factors that weigh on the decision to outsource now versus thirty-years ago.
- Oil prices are three times higher than they were in 2000 making shipping much more expensive.
- The natural gas boom in the U.S. has dramatically lowered the cost for operating an energy intensive industry here in the U.S. coupled with natural gas prices in Asia that are 400% higher.
- U.S. labor productivity has continued its consistent trend upward, which has resulted in lower labor costs that have become a smaller portion of the total cost of finished goods.
- When compared in U.S. dollars, wages in China are approximately five times higher than they were in 2000, and they are expected to continue to increase 18 percent a year.
- American unions are changing their attitudes. One such example would be GE’s Appliance Park union that was known in the 70s and 80s as Strike City. In 2005, that same union agreed to a two-tier wage scale, and today, 70 percent of the jobs there are on the lower tier starting a little over $13.50 per hour, almost $8 less than the former starting wage.
The frenzy to offshore was entirely wrong; it simply did not encompass the complete picture. In fact, labor was cheap in China thirty years ago, and so much so that it tended to compensate for a multitude of other sins. Today’s industries that manufacture are taking a hard look at where they manufacture precisely because going offshore has not given what it appeared to promise.
It is also necessary to note that manufacturing has a way of creating larger economies around them in what is called the multiplier effect. The rebirth of manufacturing here in the U.S. will not solve the jobs crisis by itself, but it will certainly strengthen the economy and reclaim many lost opportunities and skills that have been diminished if not lost in the last few decades.
In 2010, Harry Moser founded an organization called the Reshoring Initiative, which advocates that companies reevaluate all of the costs involved in manufacturing abroad as opposed to just looking at labor costs. They have developed a tool called “Total Cost of Ownership” for manufacturers to use in their evaluation. It is analogous to considering all stakeholders versus just stockholders. In doing so, it demonstrates how reshoring not only can save manufacturers money, it creates American jobs, promotes economic growth and strengthens national security.
According to Moser, “The way we see it, about 60 percent of the companies that offshored manufacturing didn’t really do the math. They looked only at the labor rate—they didn’t look at the hidden costs.”1
It appears that manufacturing firms are reevaluating their decision to offshore and now realize that in many cases, the decision was an intemperate fad as they now suffer the hangover from the offshoring frenzy.
Reference: